PCI LAB REPORT
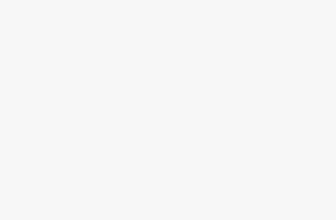
9. Portland Cement Institute - Lab Report
9. Portland Cement Institute - Lab Report
Undergoing the Coal Shortage, Do you know How much Coal reserve is remaining in the World? We had a lot of fun on coal. No? So by now, you must have known what the whole attack is ...
Energy Efficient Buildings With the current rate of urbanization and the posterior increase in energy demand energy effective structure has a significant part to play in contributing to energy ...
Water pumps are responsible for heating and cooling buildings, treating and distributing water, and generating power, which are often overlooked in conversations around smart or sustainable cities. ...
The AHU is normally a large metal box which connects to the ductwork that channels conditioned air throughout a building and returns it back to the AHU. Inside this large metal box there are a ...
"Urban heat islands" occur when cities replace natural land cover with dense concentrations of pavement, buildings, and other surfaces that absorb and retain heat. This effect increases energy ...
Keep your AC temperature at moderate to high levels in order for power saving as well as to cut your electricity bill A move by the power ministry to increase the default temperature in air ...
Builders all over the globe are gravitating towards greener technology methods that can make buildings energy-efficient and sustainable. Homeowners are also showing interest in projects that deploy ...
Natural lighting, also known as daylighting, is a fashion that efficiently brings natural light into your home using surface glazing (windows, skylights, etc.), thereby reducing artificial ...
We breath oxygen and exhale carbon-di-oxide (CO2), this is called the respiration process. When we are indoors, the level of CO2 in the air increases due to the respiration cycle. Along with CO2, ...
When insulating your home, you can choose from many types of insulation. To choose the best type of insulation, you should first determine the following: Where you want or need to ...
Light Emitting Diode (LED) and Compact Fluorescent Lights (CFL) bulbs have revolutionized energy-efficient lighting. Energy Saving LED vs CFL. CFLs are simply miniature versions of full-sized ...
Buildings and construction are responsible for 39% of global energy-related carbon emissions & contribute in more than 75 % Energy Consumption in India. With the need to save & preserve the ...
Scrutinizing a home during a watchful walk through all the areas is an easy task. What’s not so easy is determining the actual condition of the roof that lies over your head. So, when was the last ...
Insulation refers to an energy savings measure, which provides resistance to heat flow. Naturally, heat flows from a warmer to a cooler space. By insulating a house, one can reduce the heat ...
What we do and how we do it? How Econaur the only green building platform works? If you still don’t know what exactly we do, well don’t worry here you will understand what we are doing here and ...
Construction and infrastructure development are growth engines for all economies, including India’s. It is estimated that India will spend $432bn by 2030 on infrastructure development as its ...
Energy Efficiency - the subject everyone knows about but most of us don't know what to do about it. Everybody wants to reduce their energy consumption and pay less electricity bills but ...
Energy Efficiency - is a subject everyone knows about but most of us don't know what to do about it. Everybody wants to reduce their energy consumption and pay fewer electricity bills but most of ...
Whenever we talk about energy saving we always talk about changing our daily habits and go for energy-efficient appliances. But in this modern era of technology where we have more than just bulbs ...
A Energy Audit for a Building is a service where the energy efficiency of a Building is evaluated by a person using professional equipment (such as blower doors and infrared cameras), with the aim to ...